Understanding Mass Production Injection Molding: Techniques and Benefits of High-Volume Injection Molds
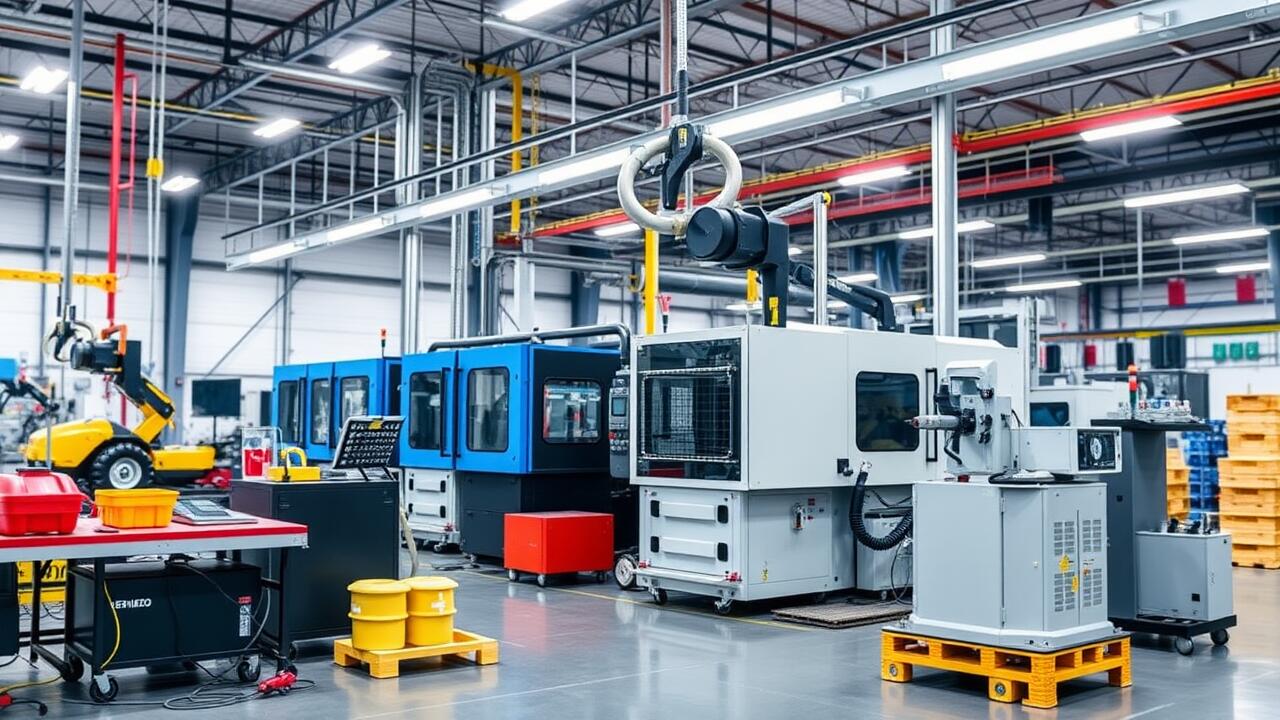
Overview of Mass Production Injection Molding
Mass Production Injection Molding is a highly efficient manufacturing process that employs specialized injection molding machines to create a vast array of plastic products. This technique utilizes precisely engineered injection molds to produce items consistently and with minimal waste. Various methods, including micro injection molding and multi-material injection molding, allow for versatility in design and functionality. The use of advanced technologies such as direct injection expanded foam molding enhances the capability of these injection moulding machines to achieve complex shapes and reduce material usage. By leveraging these innovations, manufacturers can ensure high-quality results while optimizing production costs and meeting diverse market demands.
Understanding the Molding Process
Mass Production Injection Molding is a precise and efficient method that involves injecting molten material into a custom-designed mold to create a wide range of products. The molding process begins with the injection of heated plastics into the cavity of the injection mould construction. Once cooled, the solidified plastics produce injection-molded parts that are consistent in quality and dimensions. Techniques such as micro injection moulding and multi-material injection moulding enhance the versatility of the process, allowing for intricate designs and the use of multiple materials within a single product.
Injection moulding machines play a critical role in the molding process, offering the machinery necessary to achieve the desired results. These machines operate by melting plastic pellets and injecting them into the injection molds under high pressure. The process is well-suited for high-volume production due to its speed and efficiency. Whether through standard plastics injection moulding or advanced metal injection moulding, the process consistently produces high-quality products that meet various industry standards.
Advantages of High-Volume Injection Molding
High-volume injection molding offers significant benefits, especially in mass production settings. The process involves creating injection molded parts using precise molds, ensuring consistency and uniformity across large batches. This method is highly efficient for producing plastic injection molded components, significantly reducing production time and costs compared to traditional manufacturing techniques. Reaction injection moulding enhances this efficiency by allowing for the use of various materials, resulting in more versatile applications for manufacturers.
Another advantage is the high level of scalability that mass production injection molding provides. Once the molds are created, they can be used to produce thousands of injection moulded items quickly. This aspect not only lowers the cost per unit but also ensures that manufacturers can meet market demands rapidly. Unlike hobby injection moulding, which is typically limited in scale, high-volume methods like blow molding and other advanced techniques provide businesses with the flexibility to adapt to fluctuating orders while maintaining product quality.
Types of Injection Molds
Mass Production Injection Molding encompasses various types of molds essential for achieving specific production goals. Standard injection molds serve as the backbone for most manufacturing processes, allowing molders to produce high-quality parts efficiently. Low-cost injection molds offer an economical alternative, catering to budget-sensitive projects while maintaining acceptable quality. Techniques like compression molding and rotational molding provide flexibility, accommodating different materials and designs. Specialized methods, such as double-shot injection molding and the injection moulding of liquid silicone rubber, enhance functionality and aesthetics. Each mold type is designed with a unique mold cavity that influences the final product, showcasing the diverse applications found in mass manufacturing. This spectrum of molding options ensures that businesses can select the most suitable method for their specific needs within the realm of Mass Production Injection Molding.
Standard Injection Molds
Standard injection molds serve as the backbone of mass production injection molding, facilitating the efficient creation of high-quality plastic components. With the ability to handle molten plastics, these molds are designed for durability and precision. They are instrumental in mass-producing parts where high-volume injection molding enables the mass production of intricate and uniform items. The design of standard injection molds allows for rapid cycles, optimizing the use of molten plastic to maximize productivity while maintaining consistency across batches.
The effectiveness of plastic injection molding lies in its ability to automate the process for mass production, making it an ideal choice for industries requiring large-part injection molding. Standard molds are specifically engineered to meet demanding production goals, allowing manufacturers to streamline their operations. By embracing injection molding processes, businesses can achieve significant cost efficiencies while delivering on high-volume demands. This level of automation not only reduces labor costs but also enhances the overall reliability of producing complex designs in large quantities.
Low-Cost Injection Molds
Low-cost solutions in mass production injection molding are crucial for businesses looking to optimize their manufacturing processes. These molds typically utilize simpler designs and materials to reduce costs while still being effective for high-volume injection molding applications. High-quality injection molds can be achieved without compromising on performance, allowing plastic injection molders to produce reliable products. A comprehensive injection molding guide can help manufacturers navigate the options available for creating cost-effective solutions.
Choosing low-cost injection molds does not mean sacrificing quality. Many polymer injection molding techniques enable the production of durable plastic injection molds that meet industry standards. Injection molders often explore various strategies to minimize expenses while maintaining efficiency in their first injection molding runs. Emphasizing innovative designs and materials can lead to cost-effective solutions without detracting from the effectiveness of mass production injection molding processes.
- Understand the materials: Choose materials that offer good performance without high costs.
- Explore design simplicity: Opt for mold designs that are straightforward and easy to manufacture.
- Consider production volume: Assess the quantity needed to make low-cost molds more viable.
- Implement advanced technology: Use cost-effective technologies like 3D printing for mold prototypes.
- Evaluate long-term benefits: Consider the durability and maintenance costs of low-cost molds over time.
- Work with experienced suppliers: Partner with reliable manufacturers who specialize in low-cost options.
- Stay updated on industry trends: Keep an eye on advancements that can further reduce costs without sacrificing quality.
The Role of Injection Molding Machines
Injection molding machines play a crucial role in the mass production injection molding sector, facilitating the entire molding process. These machines are designed to handle various injection moulding processes, including the use of multi-cavity injection molds and multi-shot injection molds, which enhance efficiency and productivity. The actual molding process involves the precise melting and injection of plastic into molds, allowing for the creation of complex injection-molded parts with high accuracy. By optimizing the plastic molding process, manufacturers can significantly reduce mold production costs while ensuring high-quality outputs. High-volume production injection capabilities further elevate the importance of these machines, making them indispensable in industries that rely on rapid and consistent product delivery.
Key Components of an Injection Molding Machine
An injection molding machine consists of critical components that work together to execute the manufacturing process for producing parts by injecting molten material into molds. Key parts include the injection unit, clamping unit, and control system. The injection unit melts the raw material, while the clamping unit secures the molds during the injection process. A well-designed machine enhances efficiency in mass production injection molding, accommodating simple injection molds or more complex designs. Accurate mold quality reports are essential to ensure consistent production quality across various mass production projects.
Rubber injection molding is another application where injection molding machines excel. The versatility of the machine allows for different molding methods, such as decoupled molding techniques, which help streamline the production process. Investing in robust machines that support the same mold for prototype molding manufacturing aids in maintaining mold quality over time. As manufacturers focus on mass production injection molding, the ability to adapt to varying needs while delivering high-quality results remains paramount.
Automation in Injection Molding
Automation has significantly transformed Mass Production Injection Molding by enhancing precision and efficiency throughout the process. The integration of advanced robotics allows for seamless operation, from the heating of the mold to the execution of subsequent molds. Automated systems ensure that the heated mold maintains optimal temperatures, thereby facilitating the consistent production of high-quality components. Molding professionals can also utilize automated techniques in prototype molding to create prototype molds that are essential for the initial design phase, enabling faster iterations and reduced development time.
The applications of automation extend to areas like multi-material injection, where varying materials are combined in a single mold, such as a lego injection mould. This innovative approach not only streamlines production but also allows for more complex designs that enhance product functionality. With automation, mass-producing products becomes more practical, meeting the growing demands of various industries while maintaining cost efficiency. By employing pre-hardened moulds and optimized mold design, manufacturers can significantly reduce production time and improve overall output quality.
Plastic Injection Molding Techniques
The injection process in Mass Production Injection Molding involves a carefully orchestrated series of steps to manufacture high-quality plastic components efficiently. A multi-cavitation mold allows multiple parts to be produced simultaneously, maximizing output and reducing cycle time. Precision molds are vital for ensuring that the final products meet exact specifications and tolerances. The injection machines equipped with high-speed molding capabilities utilize an injection barrel to deliver molten plastic into the mold with precision. Cost management is crucial, as mold price can significantly affect the overall budget. Implementing a prototype mold before full-scale production often aids in identifying potential issues early on. After molding, post-molding finishing work can enhance the aesthetic and functional qualities of the plastic components, ensuring they fulfill the requirements of various industries.
Comparison of Injection Moulding Processes
Different injection moulding processes serve varying applications based on production needs and material types. Mass Production Injection Molding is typically employed for high-volume manufacturing production, creating mass-produced parts with precision. Techniques like metal injection allow for the integration of metal powders into the actual moulding process, enhancing the capabilities of moulded products. Micro injection, on the other hand, focuses on producing small, intricate components, making it suitable for industries that require high precision.
The choice of injection moulding method can significantly influence the efficiency of a mass production line. For example, tandem molds can streamline the production of complex shapes in a single cycle, optimizing the workflow for mass-produced products. Companies often utilize professional mold design services to ensure that the chosen process aligns with their production goals. With advancements in technology, each variation of injection molding continues to evolve, providing manufacturers with the tools to meet diverse demands efficiently.
The Importance of Accurate Molds
Accurate molds play a crucial role in the success of Mass Production Injection Molding. The precision of the moulding process directly affects the quality and consistency of the moulded parts produced. Utilizing pre-hardened steel moulds enhances durability and ensures that the molds maintain their shape under pressure. Advanced injection machines can achieve tight tolerances and provide flexibility for complex designs, especially when dealing with custom injection projects. Employing multi-cavity molds increases productivity by allowing for multiple parts to be created in a single cycle, optimizing output and reducing mould fabrication costs.
The integration of in-mold labeling further emphasizes the importance of accuracy in mold design. This technique not only adds a layer of branding but also requires precise alignment for effective results. A skilled mould-maker understands the intricacies of the plastics injection process and can adapt molds to meet specific project requirements. As the demand for high-quality products grows, the focus on accurate molds becomes increasingly vital in Mass Production Injection Molding operations. Each element, from the choice of material to the mold design, contributes to the overall success of the injection molding project.
Benefits of Trusted Injection Molding Services
Trusted injection molding services ensure precision and quality throughout the mass production injection molding process. By focusing on the injection portion of the manufacturing procedure, these services enhance plastic part production accuracy. Utilizing advanced techniques such as micro moulding and the implementation of multi-cavity molds or stack molds, manufacturers can achieve higher efficiency in producing molded parts. The use of family molds enables a diverse range of components to be produced simultaneously, which is essential for meeting the demands of mass-producing while keeping mass manufacturing costs manageable. Reliable injection molding services not only streamline the production process but also guarantee that the final products meet industry standards and customer requirements.
Quality Assurance in Mass Molding
Quality control is crucial in Mass Production Injection Molding to ensure that each molded product meets stringent specifications. The manufacturing process involves monitoring every stage from the moment molten plastic fills the mould components to the ejection of the finished product. Ejector mould systems play an essential role in this process, facilitating the removal of manufactured parts without damage. Using high-volume injection techniques allows for the consistent quality of products, thereby reducing the likelihood of defects in production.
Implementing quality assurance practices during mould making is essential for producing durable and reliable steel moulds. A specialized manufacturing process requires detailed inspections of the mould components to guarantee alignment and functionality. Maintaining rigorous standards during production aids in identifying potential issues before they escalate. This comprehensive approach contributes to the overall success of Mass Production Injection Molding, ensuring customer satisfaction with the final molded products.
Cost Efficiency in Mass Production Injection Molding
Mass Production Injection Molding significantly reduces production costs due to its ability to create high volumes of identical moulded parts efficiently. Using aluminium moulds can lower initial tooling expenses, while many steel moulds offer durability, making them suitable for long production runs. The stack mold design allows multiple parts to be produced simultaneously, enhancing the output without increasing the cycle time. This efficiency directly impacts the cost per unit, making it a favored choice in various manufacturing sectors.
The technology behind the injection unit plays a crucial role in achieving cost efficiency in Mass Production Injection Molding. By optimizing the injection system, manufacturers can maintain consistent melt/mold temperatures, which ensures the quality of the final product. Custom moulds designed for specific applications help minimize waste and reduce the need for extensive post-processing. Overall, the integration of advanced manufacturing equipment and precise control over the injection process contributes to a more cost-effective production line, echoing the benefits of using this method in high-volume applications.
- Lower tooling costs with aluminum molds
- Durable steel molds suitable for long production runs
- Enhanced output with stack mold design
- Consistent melt/mold temperatures for quality assurance
- Custom molds reduce waste and post-processing needs
- Advanced equipment optimizes the production line
- Ideal for high-volume applications across various industries
Applications of Mass Production Injection Molding
Mass Production Injection Molding is a versatile manufacturing process widely used across various industries, including container manufacturing. This state-of-the-art injection technique allows for the rapid production of high-quality injected parts with exceptional accuracy. Employing cube mold technology enhances efficiency while ensuring that specialized injection techniques, such as multi-shot moulding, can be executed seamlessly. The precision plastic injection capabilities of typical moulds enable manufacturers to create complex geometries tailored to specific applications. As a reliable production process, Mass Production Injection Molding not only meets stringent quality standards but also adapts to the evolving needs of the market.
Industries Utilizing Injection Molding
Mass Production Injection Molding plays a vital role in several key industries, including automotive, consumer electronics, and healthcare. Companies rely on the manufacturing process fundamentals to produce components efficiently and at high volumes. Multi-shot moulds and decoupled moulding techniques are often utilized to enhance production capabilities, allowing for complex designs and multi-material parts. Companies engage screw injection machines and injection units to ensure precise delivery of molten material, meeting the demands of large-scale manufacturing projects.
This production method is not just constrained to industrial applications; hobby injection also benefits from Mass Production Injection Molding techniques. Smaller-scale projects can utilize similar principles to achieve high-quality, custom components. As industries face high-volume production needs, adopting these advanced methods becomes increasingly important. Precision and reliability in the manufacturing process enable businesses to innovate and meet consumer demands effectively.
Custom Solutions with Plastic Injection Molds
Custom solutions in plastic injection molds are crucial for addressing specific manufacturing needs across various industries. The significance of Mass Production Injection Molding comes into play as companies seek to minimize moulding defects while enhancing production efficiency. High-injection moulds can deliver precision and durability, vital for applications where quality cannot be compromised. In particular, the use of plasticized acetate injection allows for smooth processing and reduces the chances of defects in the final product, supporting large-scale manufacturing initiatives.
Customization extends beyond just the design of the moulds themselves. A moulds family design can facilitate different products through a single manufacturing method, streamlining production processes. Implementing proper mould maintenance strategies ensures that the equipment remains operational, thus reducing downtime and operational costs. As the demand for tailored solutions grows, the ability to adapt existing designs or employ alternative manufacturing techniques, such as reaction injection, becomes increasingly valuable in the evolving landscape of plastic production.
Conclusion
Mass Production Injection Molding plays a crucial role in manufacturing by converting melted pellets into high-quality plastic products efficiently. This process often employs multiple cavity moulds, which facilitate the production of numerous parts simultaneously, significantly increasing throughput. The precision and speed of Mass Production Injection Molding meet the demands of various industries, from automotive to consumer goods, ensuring that companies can deliver their products at competitive prices. Emphasizing quality and efficiency, this method remains a cornerstone of modern manufacturing strategies.
FAQS
How does plastic injection molding automate the process for mass production of plastic components?
Plastic injection molding is a manufacturing process for producing parts by injecting molten material into specialized injection moulds. This method automates the production of mass-producing plastic components, leading to high-injection molding efficiencies. With the use of high-speed molding machines, injection molded plastic items can be produced in high volumes. In recent advancements, fusible core injection moulding and double-shot injection moulding techniques have further enhanced the capabilities of conventional moulding processes, allowing for greater design flexibility and complexity in mold harder materials.
What are the advantages of using different types of injection moldings in mass producing plastic components?
Different types of injection moldings, such as plastic injection moulding and rubber injection moulding, offer several advantages for mass producing components. These techniques, including high volume injection and simple injection moulds, enhance efficiency and precision in production. By utilizing various moulds family moulds and specialised injection methods, manufacturers can significantly streamline plastic production processes, especially as plastic injection molding automates the process for mass production, ultimately leading to cost savings and improved product quality.
What is the impact of injection-moulded products on the efficiency of plastic production compared to methods like extrusion moulding and additive manufacturing?
The impact of injection-moulded products on the efficiency of plastic production is significant, as injection molding provides faster cycle times and higher precision compared to other methods like extrusion moulding and additive manufacturing. While mold refers to the cavity that shapes the plastic parts, the use of injection-moulded components has greatly enhanced production capacity, leading to a point where plastic production overtook traditional manufacturing methods in many industries.
How can companies ensure the quality of plastic components produced through mass production injection molding?
Companies can ensure the quality of plastic components produced through mass production injection molding by implementing strict quality control measures, using high-quality materials, and conducting regular maintenance on injection molding machines to prevent defects and inconsistencies.
What are some common defects that can occur in plastic components produced through mass production injection molding?
Some common defects in plastic components from mass production injection molding include warping, sink marks, short shots, flash, and surface blemishes. These defects can arise due to factors such as improper mold design, incorrect temperature settings, and insufficient material flow, impacting the overall quality and functionality of the injected products.